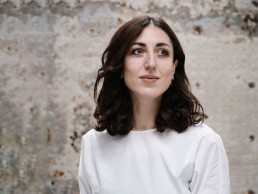
Oksana Bondar
Oksana Bondar, Director of Design at Biohm, is a Russian designer and innovator. She sits down with darc Editor Sarah Cullen to discuss her journey from marketing and PR into bio-engineering design for sustainable products for the home.
Growing up in Perm, Russia, but born in Taldykorgan, Kazakhstan, Bondar began her professional career in marketing PR and media. “Product design and industrial design, which I was obsessed with, wasn’t an option in Russia, hence my other creative choices took me to marketing,” she tells darc. Pursuing this avenue, Bondar moved to Prague to complete a Bachelor’s degree in Communications, Mass Media & PR at The University of New York. She then moved to the UK and rediscovered her design-led passion. Here she completed a second degree in Product and Furniture Design at Kingston University in London. “It was in the UK that I discovered the design discipline and had to go back to uni to re-study,” she reflects.
A core value that has run through Bondar’s life is to be as resourceful and kind to the planet as possible. “The passion to change things for the better has been with me all along. It was when I was at uni that I started looking into my professional industry and realised how incredibly damaging and destructive it is. For me, being very passionate about making things to be better meant I couldn’t go down the route of normal design practice. I believe designers and materials and the materiality of things are interconnected.”
A few years ago, Bondar attended a talk held at the Design Museum, London, by Artist Zoe Laughlin, which sparked a realisation of the type of designer she wished to be. The talk revolved around designers who are farmers of their own material. “That was exactly how I would identify myself. You become an innovator, because you are looking into ways to turn abundant waste matter into something that is valuable using all your traditional training as a designer. Then, the more you learn about it, the more you understand it’s not just about waste, it’s far bigger than that. It’s about biomimetics and ways that nature solves these problems. There’s no need to reinvent the wheel! All these solutions are out there, we just need to learn to look for them. In nature, waste is non-existent. When something perishes, it becomes fit for something else – for a new life, and it’s continuous circles.
“That was my journey. All of my work started from uni, and since then has evolved around innovative materials derived from waste and transforming waste streams,” she explains.
Bondar went on to be the Co-Founder of Luna Lab, a circular design studio that aims to design out waste and reimagine products, services, and system. She then joined Biohm, firstly as the Business Innovation Manager, and then onto the Director of Design.
Biohm is a London-based innovation studio that was founded by Ehab Sayed, a designer, engineer, researcher, and entrepreneur, to bring the principles of biomimetics into the construction industry by adapting and applying the ingenuity that is found in nature to our built environment. Its aim is to revolutionise the built environment, and the way businesses are conducted, through the development of bio-based materials, circular construction systems and innovative business models. At a time of climate crises, it believes radical change is needed, requiring systemic innovation on a large scale to re-address the multifaceted issues interwoven in economies that have led us to where we are now.
“If we are to venture beyond merely reducing our impact on the planet and our health, contemporary approaches to waste management, manufacturing and building must undergo a step-change towards having a positive and regenerative impact,” says the studio.
“Our goal is not only to build a successful company, but moreover, to improve the quality of people’s lives through enabling the use of healthy, environmentally friendly, circular materials and building solutions for applications across the design and construction industries, eliminating the concept of waste and demonstrating how business can equitably and ethically work in collaboration with the natural world, industry, academia, government and community.”
More than 5,000sqft of space is dedicated to Biohm’s warehouse, lab, and offices, which together form a biomimetic research hub. Working with industrial partners, it repurposes waste materials and industrial by-products into useful materials. Whether it is through myco-remediation processes or using its unique Orb binder, it now works with a wide range of organisations across London, including a number of councils, research institutes, educational institutes and businesses.
It produces two unique materials: Mycelium and Orb. Mycelium – the vegetative filament root structure of mushrooms – is used to grow Biohm’s materials using organic and synthetic substrates that are the by-products or ‘wastes’ of other industries. This material has been used to create the world’s first accredited mycelium insulation product.
Orb – organic refuse biocompound – is manufactured from difficult to reuse or recycle by-products, utilising resources that would otherwise go to landfill. Biohm converts one of the world’s fastest growing waste streams – food waste – into valuable and functional materials that can be moulded to create 3D products. Orb is 100% biodegradable, vegan, sustainable, and renewable.
“Biohm was established just five and a half years ago,” says Bondar. “Founder and Director of Innovation, Ehab Sayed is my personal twin – I have never met a person who was so like me. We finished each other’s sentences, it was that kind of connection.
“He established Biohm for various reasons, but it started for him back when he was doing his Master’s in engineering. The design profession evolves a lot around problem solving, or finding better solutions to problems, or better ways of doing things. The problem he was looking into was waste and waste in construction.
“That evolved into the solution and construction system that had biomimetics embedded into the design, but it was also solving the problem of waste, as in on-site waste, waste when buildings are being built as well as when buildings are being demolished,” she continues.
Bondar recounts that once Sayed began prototyping and evolving his construction system, he realised the materials he was working with were either produced by “greenwashing brands or products that were deemed eco”, but when researched further, they were sometimes proven to be “worse than synthetic materials or plastics”.
This ethos of sourcing or creating unique materials that are truly eco-conscious is something that runs through all the team members at the Biohm studio. The current team is formed of people from various professional backgrounds including designers, engineers, scientists, and lawyers with business backgrounds. “We all start from a point where we’re obsessed and passionate about the problems and finding the solutions. And the problems and threats are to all the creatures and life that walks the earth. Waste is just one of the prominent ones,” explains Bondar. “That’s what’s beautiful about Biohm and how it came about. It aligns with an individual’s passions and ideas and impacts that we all want to achieve.”
When asked about how she accrued all her technical knowledge after jumping career paths from media to design, Bondar expands: “I came into Biohm when it was fully established, having gone through the same journey myself previously. That’s why it was such a beautiful merge because I was doing the same thing, just separately.
“In the early days, I was researching and studying myself; it was self-taught chemistry and biology. And then I would reach out to people when I was stuck. I remember when I was experimenting with materials at uni, I reached out to the chemistry department for help and got a great response. People were fascinated because it’s not often they end up in a room with a designer. I also needed help to build a machine, so I went to the engineering faculty where Formula One cars were built. There I was with a little design for a shredder and asking questions about a motor I had bought from eBay that came from a conveyor belt!
“I think it’s an agility and passion that drives you either to reach out or pick up a book. And, I think it’s fascinating that suddenly your design becomes ever more important and valuable, because it’s no longer aesthetics or trends that define it.”
Mycelium insulation is the primary export from Biohm, however last year it launched its first ever commercial product, a lighting range, that harnessed its unique and sustainable materials. The Obscure lampshades are created using its Orb material, consisting of orange peel and coffee chaff (the outer skin of a coffee bean that is removed when roasted). Wanting to expand their expertise into objects that are more accessible to wider markets and are suitable for homes, offices, restaurants, and more, the team’s first instinct was to create a light product. Bondar expands: “Lighting was the first option because it seemed an easy-ish product to look into in terms of matching our material and our capacity to design and produce it.
“We began by looking at how nature forms things. For example, when leaves get wet, they become moldable and take the shape and form of what they wrap themselves around. That, in addition to gravity and all other natural forces that surround us, impact the various matters into a shape. And that’s exactly how our lampshades are made.
“Typically, shapes are created when matter is injected into a mould, but for us our mould is like a skeleton. The material is layered on top of it, and it forms itself. This means each lampshade is completely unique, and in some ways design-less. This is how biomimetics comes into the design; nobody is holding or forcing the shape.
“Designing becomes very involved and as the designer you are the driver that determines the shape and finish; you determine everything. For us it’s not an ego-driven approach, it’s more of a collaboration with the material that we are respectful towards.
For the Obscure collection, a local office building approached approached Biohm with an abundance of orange peel as a waste product from their high production of fresh orange juice. “Orange peel is very problematic,” says Bondar. “You wouldn’t think so, but it is due to its acidity; it can’t be composted because it destroys pH levels in soils. But, for us it works amazingly well because of the chemical composition. It’s got peptides and other chemical compounds in there that makes it elastic. So for lampshades, when you work with it when it’s not cured, it’s kind of rubbery. It likes falling and forming and shaping over things, it’s just brilliant. The colour is quite interesting as well because usually natural materials are very earthy, this one is a little different. We’re also looking into pigmenting it as well and developing a bit of a colour palette.
“Coffee chaff is the same, it too is very acidic. This material is incredibly beautiful and has such a deep chocolate colour, and to work with it’s more leather-like. You could see when it forms itself, in the crevices, they actually have wrinkles like an elephant foot – they have such unique personalities,” she describes.
In order to turn the waste substrate into a workable material, Bondar explains the various techniques they use including chipping or granulating. Coffee chaff doesn’t need to be processed as it is suitable in the form it already arrives in, whereas fresh orange peels need to be broken down into smaller pieces. These elements are then combined with a bio-based binder as a hardening component that the studio developed. This ensures the product is completely natural, and even ranked as food-grade, although Bondar doesn’t recommend eating it because “you would break your teeth”. This part is then combined with a filler, fibrous cellulosic substrate to form the final material used to create the lampshade.
“Once the lampshade is formed, it is then cured. This can be done simply via air-drying or to meet our target of batch production, we custom-made a dehydrator that is super low on energy consumption; it’s not an oven or a kiln. It just speeds up the drying process.”
Mycelium is a secondary material that the studio is experimenting with to produce a follow-on lighting collection that is scheduled to be launched later this year. Mycelium is a living, breathing, moving and growing organism that will present a very different final product. Again, lamp production will follow a similar process to that of the Orb-based Obscure collection, as the mycelium material has a character of its own; it cannot be forced into a mould, yet will form naturally, growing inside a mould. “ The concept was called self-formed finding; it’s a biomimetic approach to design,” explains Bondar. “In nature, when cells or bubbles in water accumulate, they start to form themselves and accumulate. “It’s very complicated – I was reading biology books and discovering how things grow and form in nature – and then I looked into the root concept and how I could use that in what we do here at Biohm.
“It’s matter with other matter,” she continues. “And because of the properties of the material, it is a structural and dense form that can also act as an acoustic absorber.
“The Mycelium lamps are currently prototypes, with final prototypes ready at the end of this month.”
For the time being, the team will continue to use both the coffee and orange materials due to the high quantities of local waste streams available to them. However, with a strong recipe in place, the possibilities of exploring other bi-product waste substrates is always an option to create variations of lampshades.
With a strong focus on the production of the lampshade materials, the other components of the lighting fixture as a whole were also a large consideration in the beginning of the design concept. “The brief was so ambitious that we actually weren’t even looking into light sources at the beginning. There are so many mushroom species, for example, and some that are bioluminescent. We were looking into ways to not have electrical lighting, but instead maybe tap into the ability of an organism to glow in the dark,” she explains. “We also looked into the natural ability to bounce light. But we realised a lot of that was very complex and would need years of research and development, so it was parked.
The use of natural-based materials could be a concern for some in terms of the product’s longevity, but Bondar reassures that the material is made to last. “I don’t have a number for longevity, but our products go through in-house and third party testing against relevant standards and mechanical properties,” she explains. “The lampshades have gone through mechanical testing and flexural strength testing. The material has similar properties to plywood and mdf if the waste stream is fibrous. So it’s very strong, it’s not going to just crumble and fall apart.
“Furthermore, in-house we test for environmental conditions. The lamps will sit in a tent with 88-90% humidity and a lot of heat, and they’re absolutely fine – it’s crazy!
“These are not realistic environments however; we wouldn’t recommend people to take them into the tropics or under rainfall. They’re not IP-rated so not suitable for bathrooms or outdoors. We’ve also done impact testing by throwing it down and bumping into it and it’s proven to be a very sturdy material. These are all stress tests to push the product to its limits.
“In terms of the mould, again, we do a bio-resistant test where we expose materials and products to contaminants. They sit in a chamber with mould, yeast, and a lot of bacteria. The orange peel and coffee chaff, because they have a lot of natural acids, repel all bacteria and mould naturally.
“We also have a natural top coat we add that is a mixture of linseed oil and beeswax that protects it further, although we are trying to replace beeswax with plant-based wax or just oils.
“The way these materials behave is very similar to wood. If you were to get it wet, it would mark and potentially grow things – or like an outdoor table, for example, typically has things growing on it. It just needs a bit of extra care or housed in an environment that it thrives in. It also inspires good culture for a respectful attitude to things around us.
“If you did change your mind or re-decorate, Biohm takes materials and products back. The Orb material can be shredded down and re-moulded, so it’s infinitely recyclable; or it can be recirculated either back into a lampshade or something else. And Mycelium is the same, but it eats itself! It would find nutrients in itself as a cured material, shred it up, feed it back to the life organism and it would consume it. For us, it’s a value to take a product back and use it as a substrate again.
“The trend in recyclable fashion – as long as there’s businesses and systems, infrastructure, and technology, and places to deal with it – is fine. But at the moment, current materials, infrastructure and tech is not fit for that and that’s why longevity is a bit of a playing card. It’s the same when you look at nature – seasons change, trees lose their leaves and they grow back again. The change, trend and fashion is there, but it’s not too shameful so long as we can deal with the cyclical trends.
“The world is different to what it was 5 years ago,” she continues. “My work used to be called art because it was funky; nobody saw a reason to do it. But, as a company, we are speaking to some of the biggest multinational companies that are looking for answers to questions that we have been talking about and working on for a long time. We are now the key holders. People are interested and passionate about it, they want to change.”
In terms of sourcing all of the components for light fixtures, Bondar claims it has been a painful experience to find products that match their strict sustainable ethos. “There is not much out there that matches our militant our approach or ambition,” she says. “We have been looking into wooden fixtures, lampholders, as well as ceiling roses, but I’m always suspicious of what people declare their product as, and tracing down the supply chain can be difficult. They could say that they’re working with European companies, but actually their components are made in China. So all of a sudden, your product or the components that you’re getting from your partner, company or supply, actually have a breached supply chain.
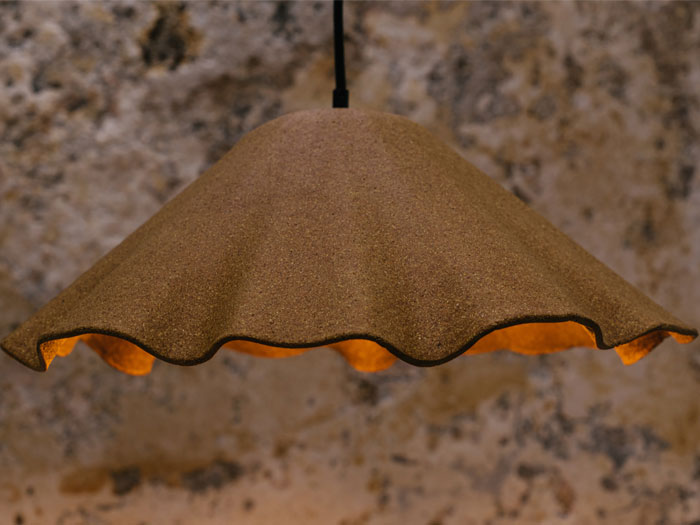
“We’ve procured as militantly as we can for now, but we always plan to build on that, and keep a close eye on what’s available. This is not something that we do, and maybe can’t do. But coming across new technology like OLED excites us, but they’re not readily available to us at the moment.”
Moving forward, Biohm is opening a new warehouse facility on the outskirts of London. The space is mainly dedicated to the production of its insulation products, however the hope is for embedding other product lines and technologies in one large factory space.
“The big idea is starting with the Mycelium insulation but then potentially having hubs, hyper-localised (zero travelling miles) everywhere. That means we are able to draw on the local waste streams as well as help communities thrive and take control of their prosperity locally.
“However negative Brexit is, it does kick-start this sense of pride and not turning your eye far away but looking right in front of you and seeing how amazing it is. Individuals and professionals turning back into their communities is fabulous! We call it ‘Glocal’ – working with local formulas, systems and ways of working but implementing globally. By doing so, you have figured out how to set up a manufacturing facility that draws on local resources, waste streams and people, and give them the power to do it and make money for themselves and livelihoods, as well as play in the economy and industry. That model can work anywhere in the world.
“We are still finding our feet for ways of distributing, or wholesaling, or sending our lighting products to a design shop to retail them. I think we will launch within our own network for the time being, but we also want to give people the opportunity to experience the materials, innovation and products. We are looking into hosting a once-a-month open door event as we have a lot of requests for a showroom experience. Hopefully there will be an option to do a product launch on one of these evenings,” she concludes.
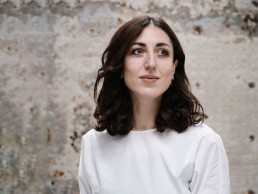